Composite Production
Composite Production
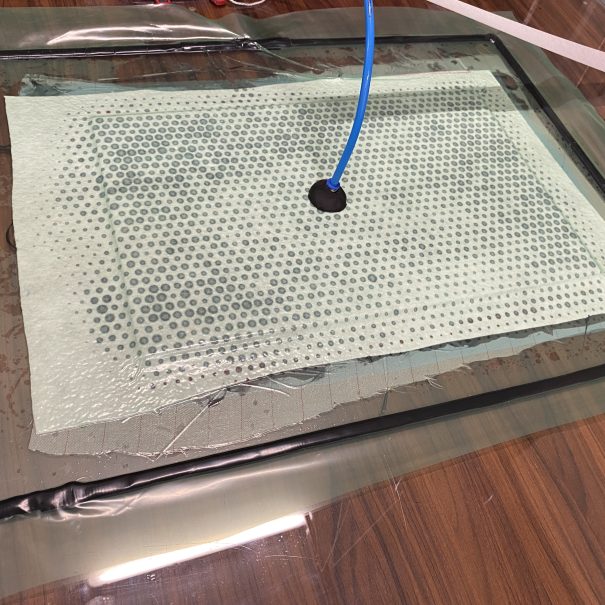
We can produce your Unmanned Aerial Vehicle and similar geometry part designs as composite. Composite material is used especially in the field of aerospace to produce complex parts in a lightweight and durable way.
Composite production is the process of combining reinforcing materials such as carbon fiber, glass fiber and aramid (kevlar) with resin and reinforcing materials. As a result of this production, lighter productions with similar strength compared to metal materials can be realized. For this reason, it is used in many areas where light weight is important, such as aviation, defense industry, racing sports.
You can choose from different composite production processes such as wet lay-up, vacuum infusion and prepreg. Part production cost and time are determined after your meeting with our team, as they depend on the desired features and design.
You can contact our team and plan the production processes to produce your designed models with composite materials. You can get detailed information about composite production processes below.
Material Selection
Carbon fiber, glass fiber materials and epoxy resins are generally used in unmanned aerial vehicles. In addition to these, it is also possible to use reinforcement materials. Reinforcement materials and epoxy-based matrix materials hold the part together, provide load distribution and increase the strength of the composite material. It is very important that the material to be selected is selected in accordance with the production method and duration and that the application rules are followed. The quality of the materials to be used determines the strength of the part to be produced.
Mold Preparation
Molds made of polyester, epoxy or aluminum material are made suitable for part printing by applying mold release agent after surface cleaning. Depending on the production method, carbon fiber, glass fiber reinforcements and resin are prepared in appropriate quantities and sizes.
Composite Production
The prepared reinforcement fabrics and resin are applied to the mold surface according to the application technique. After the application, the part is vacuumed with the mold and the part is adhered to the mold surface. The composite part is compressed to increase resin absorption and remove air bubbles. A special vacuum system and equipment is used for the vacuum process. Then a certain time is waited for the resin to harden and cure. This time varies according to the resin type.
After the curing process, the part is removed from the mold.
Mounting
The part removed from the mold is cleaned by cutting the excess edges. If the part to be produced consists of 2 components that need to be combined, the part assembly process is performed with the help of two molds. Then production is completed in one piece. Finally, surface cleaning and sanding processes are performed and the part is delivered to you. Since the cost and duration of part production depends on the desired features and the design to be produced, it is determined after your meeting with our team for more detailed information.